Mobile Concrete Batching Plant
Output:
25 – 120(m³/h)
Total Power:
60.8 – 160(kw)
A mobile concrete batching plant is a key machine. It produces concrete on-site. It can move easily between different work locations. This makes it very useful for changing project needs. This plant offers fast setup and quick relocation. This saves time and money for your projects.
Mobile Concrete Batching Plant is a type of equipment capable of integral or split transportation, rapid installation and disassembly, and concrete production at different construction sites. Simply put, it integrates a complete concrete batching plant (including all functions such as aggregate batching, weighing, mixing, and control) onto one or several trailer chassis, giving it high mobility and rapid deployment capability.
Table of Contents
- What Core Advantages Does a Mobile Concrete Batching Plant Offer?
- What Main Modules Make Up a Mobile Batching Plant?
- How Do You Choose the Right Mobile Batching Plant Model and Capacity?
- How Does a Mobile Batching Plant Achieve Fast Installation and Relocation?
- What Are the Investment and Operating Costs of a Mobile Concrete Batching Plant?
- What Are the Daily Maintenance Points for a Mobile Concrete Batching Plant?
- Which Engineering Projects Are More Suitable for Adopting a Mobile Concrete Batching Plant?
- FAQs
What Core Advantages Does a Mobile Concrete Batching Plant Offer?
A mobile concrete batching plant is a highly integrated machine. It can be quickly set up and taken down. It moves easily to different construction sites. It combines all key functions of a stationary plant. This includes aggregate batching, cement storage, water mixing, and control systems. All these parts are on one or more towable chassis. This makes it very easy to move and deploy on site.
The biggest advantage is its flexibility. It allows for on-site concrete production. This reduces the need for long-distance concrete transport. It saves time and money. It is perfect for projects that move often or have limited space.
Key Benefits of Portable Concrete Equipment
The main difference between a mobile plant and a fixed one is its high mobility. This makes it very valuable for many projects.
Integrated Design: The main body of the plant is on one trailer. This includes the aggregate batching system, conveyors, mixer, water system, and control room. Some larger models might have separate mobile units for cement silos.
- Fast Setup and Teardown: The plant uses a modular design. It has quick connections. Many parts are pre-assembled. Hydraulic lifting systems or simple cranes can quickly set it up. It can start producing concrete within hours or days.
- Easy Relocation: A tractor truck can tow the entire plant or its main modules. It moves quickly via road transport to new sites. This makes it a portable concrete batching plant.
- Automated Control: It has an advanced PLC control system. This system ensures precise material measurement. It automates the mixing process. It also records data and diagnoses faults.
Advantage | How It Helps You | Your Direct Benefit |
---|---|---|
High Mobility | Moves easily between sites | Reduces transport costs, quick deployment |
Fast Setup | Minimal foundation needed, quick assembly | Saves time and money on site preparation |
On-Site Production | Concrete made where it’s needed | Fresh concrete, less waste, better quality |
Cost Efficiency | Lower transport costs, faster project completion | Higher profit margins, better budget control |
What Main Modules Make Up a Mobile Batching Plant?
A mobile concrete batching plant is designed for integration. It packs all main functions of a stationary plant into a movable setup. Understanding its modules helps you see its compact power. This design makes it a true mobile concrete equipment.
Each module plays a key role. They work together for efficient on-site concrete production. Their compact layout helps with quick deployment and easy transport.
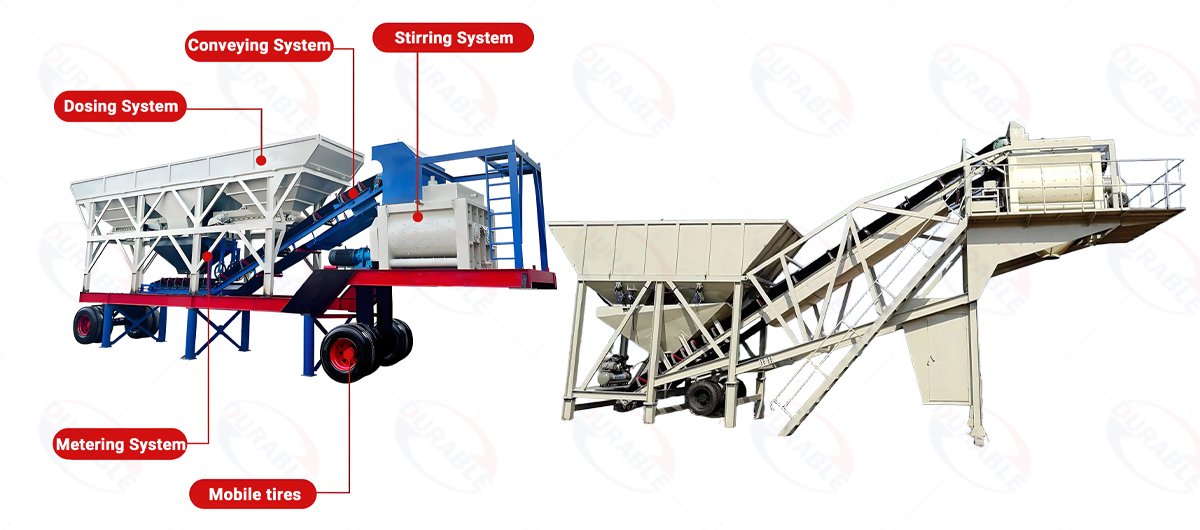
Core Modules of the Mobile Mixer
Our mobile concrete batching plants are known for their great mobility and fast setup.
Wheeled Chassis Design: The whole plant’s main structure sits on a strong chassis. This chassis has wheels and a towing hitch. A truck head can pull it directly. No special transport tools are needed. This is the heart of the mobile搅拌站 (mobile batching plant) concept.
- High Integration, Small Footprint: All core function modules are integrated. The structure is compact. This reduces the plant’s footprint. It needs less space on site.
- Fast Setup and Commissioning: The design uses pre-connected wires and pipes. It has folding or hydraulic lifting features. Most connections are quick-fit. Only a few people and simple tools are needed for assembly and testing. It can start production in hours or days.
- No Complex Foundation Needed: It usually only needs flat, firm ground. It does not need large concrete foundations. This saves time and money on groundwork.
Reliable Production and Concrete Quality
Our mobile plants deliver consistent performance.
High-Precision Metering System: Even for a mobile plant, we use top international brand sensors. We use weighing instruments. They have advanced auto-compensation. This ensures precise measurement of aggregates, powder, water, and admixtures. This guarantees accurate concrete mix ratios.
- Efficient Forced Mixer: We use high-quality twin-shaft forced mixers as standard. They mix evenly and efficiently. They can produce concrete of all grades. Mixer arms and blades use high wear-resistant alloy materials. This ensures a long service life.
- Automation and Smart Control: The advanced PLC control system stores recipes. It manages production data. It diagnoses faults. It allows remote monitoring. It is easy to use. It needs less skilled operators.
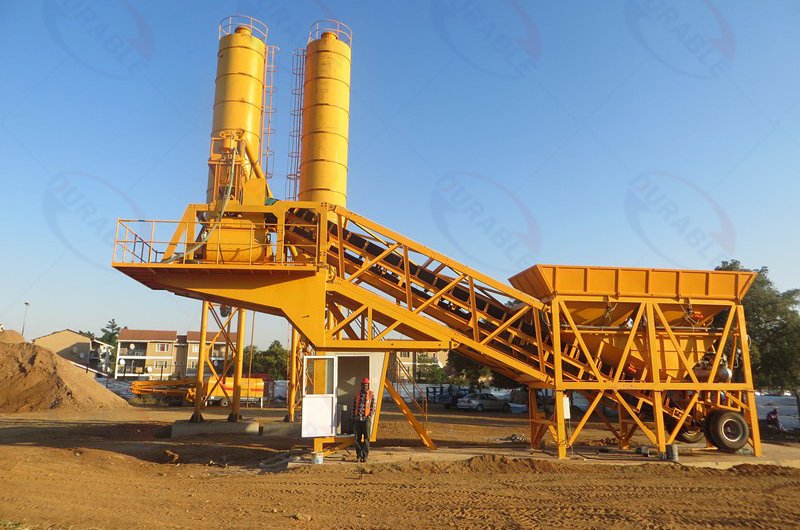
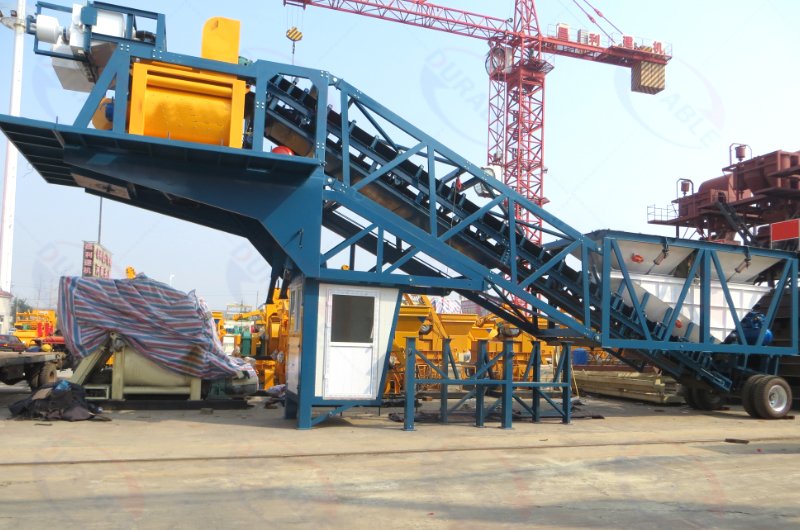
Module System | Key Component/Function | Your Operational Advantage |
---|---|---|
Chassis & Frame | Wheeled, robust structure | Easy transport, quick setup |
Aggregate Batching Unit | Weighing hoppers, feeders | Precise material measurement |
Mixing Unit | Twin-shaft mixer, wear-resistant parts | High-quality, consistent concrete |
Control Room & System | PLC control, user interface | Automated operation, data management |
Auxiliary Systems | Dust collectors, pneumatic components | Clean operation, reliable function |
How Do You Choose the Right Mobile Batching Plant Model and Capacity?
Choosing the right mobile concrete batching plant involves matching its features to your project. You must consider the project’s size. Also, think about how long it will last. You need to pick a model with the correct mobile batching plant capacity. This ensures efficient on-site concrete production.
The right choice affects your project’s speed and cost. It ensures you have enough concrete. It also avoids buying a plant that is too big or too small.
Factors for Capacity and Model Selection
When selecting a mobile batching plant, consider these key factors:
Project Concrete Volume: Estimate the total concrete needed for the project. For example, a 50,000 cubic meter project will need a different plant than a 5,000 cubic meter one.
- Project Duration: For short-term projects (a few weeks or months), a smaller, very quick-to-deploy model might be best. For medium-term projects (6 months to 2 years), a higher capacity model might be better.
- Daily/Hourly Demand: Calculate the peak concrete demand per day or hour. Match this with the plant’s mobile batching plant capacity. Our models range from 25m³/h to 120m³/h. Choose a plant that can meet your peak needs without overworking.
- Site Mobility Needs: How often will you move the plant? If very frequently, a highly integrated, single-trailer model is best. If less often, a larger, multi-module plant might be fine.
- Site Space and Ground Conditions: While mobile plants need less foundation, a level, firm area is still needed. Ensure the plant footprint fits your site.
- Local Regulations: Check any local rules for plant size, emissions, or noise. This might affect your model choice.
- Budget: Balance the plant’s purchase price with its features and capacity. Remember to consider long-term operating costs.
Technical Data:
Model | YHZS25 | YHZS35 | YHZS50 | YHZS60 | YHZS75 | YHZS90 | YHZS120 |
Mixer | JS 500 | JS 750 | JS 1000 | JS 1000 | JS 1500 | JS 1500 | JS 2000 |
Mixer capacity | 0.5m³ | 0.75m³ | 1m³ | 1m³ | 1.5m³ | 1.5m³ | 2m³ |
Output | 25m³/h | 35m³/h | 50m³/h | 60m³/h | 75m³/h | 90m³/h | 120m³/h |
Aggregate bins capacity | 4*2.3/2*4.6m³ | 4*2.3/2*4.6m³ | 4*5.6/2*11.3m³ | 4*5.6/2*11.3m³ | 4*5.6/2*11.3m³ | 4*6.5 m³ | 3×20 m³ |
Discharging height | 3.8m | 3.8m | 4.1m | 4.1m | 4.1m | 4.1m | 4.1m |
Control | Full Automatic Control | ||||||
Aggregate | 2% | 2% | 2% | 2% | 2% | 2% | 2% |
Cement weighting | 1% | 1% | 1% | 1% | 1% | 1% | 1% |
Water | 1% | 1% | 1% | 1% | 1% | 1% | 1% |
Additive | 1% | 1% | 1% | 1% | 1% | 1% | 1% |
Max aggregate | 60mm | 60mm | 80mm | 80mm | 80mm | 80mm | 80mm |
Max hauling speed | 8km/h | 8km/h | 8km/h | 8km/h | 8km/h | 8km/h | 8km/h |
Working dimension | 16.7*2.73*5 | 16.7*2.73*5 | 19.3*3.2*7.5 | 19.3*3.2*7.5 | 20.3*3.3*8.5 | 20.3*3.3*8.5 | 30.2*3.4m*9 |
Power | 60.8kw | 72.3kw | 92kw | 92kw | 102kw | 120kw | 160kw |
Total weight | 14.66t | 22t | 26t | 26t | 29t | 33t | 38t |
How Does a Mobile Batching Plant Achieve Fast Installation and Relocation?
A mobile concrete batching plant is designed for speed. Its construction allows for quick setup and movement. This makes it ideal for projects that change locations often. The secret lies in its modular and integrated design. This design leads to rapid concrete production wherever you need it.
This fast deployment capability is a major advantage. It reduces project timelines. It also lowers the costs linked to long-term site setup. It is a key feature of any quick deployment batching plant.
Features for Quick Setup and Movement
Our mobile concrete batching plants are built for speed. They minimize setup time. They also simplify relocation.
Pre-Connected Components: Many parts are pre-installed at the factory. This includes electrical cables and water pipes. They use quick connections. This means less wiring and piping work on site.
- Folding and Hydraulic Design: Key structures like conveyors or mixing units can fold. Some have hydraulic systems. These lift and position the components automatically. This reduces the need for cranes or heavy lifting equipment during setup.
- Integrated Main Unit: The core parts are on one or two main chassis. This means fewer separate loads for transport. It simplifies the assembly process on the new site.
- Minimal Foundation Needs: Unlike fixed plants, mobile plants usually only need a flat, firm area. They do not need deep or large concrete foundations. This saves weeks or even months of groundwork.
- Wheeled Portability: The plant’s main body has wheels. A standard truck can tow it. This allows quick highway transport. You can move it from one project to another easily. This makes it a true mobile concrete equipment.
The combination of these features means a mobile batching plant can be running in a new location much faster. This can be in hours or a few days. A fixed plant could take weeks or months. This speed means projects start producing concrete sooner. It saves significant time and money.
What Are the Investment and Operating Costs of a Mobile Concrete Batching Plant?
Understanding the investment and operating cost of a mobile concrete batching plant is key. It helps you see your full return on investment (ROI). While the initial cost can be higher than just buying concrete, the long-term savings are significant. This is especially true for projects needing on-site concrete production.
The total cost includes purchase, setup, and running expenses. It also includes maintenance. A well-chosen mobile plant can lead to substantial savings. It also boosts project efficiency.
Analyzing the Costs and Returns
Initial Investment: The purchase price of a mobile concrete batching plant varies. It depends on its capacity, features, and brand. Generally, it’s a significant upfront cost. However, compare this to the cost of buying ready-mix concrete over a project’s life. Also, consider the cost of building a temporary fixed plant. A mobile plant often has a lower overall project cost for temporary or multiple sites.
- Setup Costs: Mobile plants have much lower setup costs than fixed ones. They need minimal or no concrete foundations. This saves on materials and labor for groundwork. Their quick assembly also reduces installation time and associated labor costs.
- Transport Costs: Moving the plant incurs transport costs. But these are offset by reduced concrete delivery fees. Instead of many trucks bringing concrete from afar, one plant produces it on site. This lowers fuel and driver costs significantly for concrete transport.
- Operating Costs: These include fuel or electricity for the plant, labor for operators, and raw materials (aggregates, cement, water, admixtures). Efficient models with smart control systems can reduce material waste. They also use less energy.
- Maintenance Costs: Like all heavy machinery, mobile plants need regular maintenance. This includes routine checks, lubrication, and replacement of wear parts (like mixer blades). Our plants use durable components. They are also designed for easy access. This helps keep maintenance costs low.
- Reduced Logistics Costs: By producing concrete on-site, you reduce long-distance concrete delivery. This cuts down on fuel, vehicle wear, and driver hours for transport. This is a major saving for remote or spread-out projects.
- Increased Project Efficiency: Fast setup and on-site production mean projects start and finish faster. Reduced delays lead to significant financial savings. This also frees up your team for other tasks. This boosts overall productivity.
What Are the Daily Maintenance Points for a Mobile Concrete Batching Plant?
Daily maintenance is crucial for your mobile concrete batching plant. It ensures the plant runs reliably. It also extends its service life. This prevents unexpected breakdowns. It also helps maintain consistent concrete production quality.
Regular checks and prompt actions are key. They keep your plant in top working order. They also ensure safety on the job site. Following these simple steps can save you time and money.
Essential Daily Care for Your Mobile Mixer
To keep your mobile concrete equipment running efficiently, follow these daily maintenance points:
- Pre-Operation Check: Before starting, check all material levels. This includes aggregates, cement, and water. Look for any visible damage or loose connections. Ensure all safety guards are in place. Test emergency stop buttons.
- Mixer Drum Cleaning: This is the most critical step. Clean the mixer drum thoroughly after each shift. Leftover concrete will harden quickly. This can damage the mixer. Use the integrated cleaning system with high-pressure water.
- Conveyor and Hopper Cleaning: Clear any material buildup from conveyors, hoppers, and discharge chutes. This prevents blockages. It ensures smooth material flow.
- Lubrication Check: Ensure all moving parts are properly lubricated. Check grease points for bearings and rollers. Top up lubricants if needed.
- Water and Air Systems: Check water hoses and pumps for leaks. Ensure the air compressor works correctly. Look at air lines for any damage.
- Dust Collection System: Inspect the dust collector. Empty dust bins if full. Clean filters regularly. This keeps the air clean. It also ensures the system works efficiently.
- Control Panel and Electrical: Check the control panel for any error messages. Ensure all lights and indicators work. Inspect electrical cables for wear.
- Structural Integrity: Look for any new cracks or damage on the main chassis and support structures. Address any issues promptly to prevent major structural failures.
Practical Tips and Advice: - Consistent Schedule: Create a daily maintenance checklist. Stick to it every day.
- Operator Training: Train all operators on daily maintenance tasks. They are the first line of defense against problems.
- Log Book: Keep a logbook for all checks and maintenance performed. This helps track issues and service history.
Which Engineering Projects Are More Suitable for Adopting a Mobile Concrete Batching Plant?
Mobile concrete batching plants are ideal for specific types of projects. They excel where flexibility and quick deployment are key. Their ability to move and set up fast makes them perfect for certain engineering tasks. They allow for efficient on-site concrete production. This reduces transport costs and ensures fresh concrete.
These plants are a great fit for projects that are spread out. They also work well for projects with limited duration. They are perfect for sites where building a permanent plant is not practical.
Ideal Projects for Mobile Batching Plants
Mobile concrete batching plants are the best choice for these B2B client types:
Linear Engineering Projects: These include highways, railways, airport runways, long-distance water transfer projects, bridges, and tunnels. These projects need concrete along long stretches. The plant can move as construction progresses.
- Short-to-Medium Term Projects: These are projects with a high demand for concrete but a limited duration. Or, they are projects that need quick site clearance after completion. A mobile plant saves money on permanent setup and teardown.
- Multi-Site Operations: Companies with several small or medium-sized projects can use one mobile plant. Its flexibility allows quick movement between different construction sites. This optimizes resource use.
- Infrastructure Construction Companies: This applies to construction in transport, water conservancy, and power sectors.
- Mining Companies and Contractors: Large construction projects within mine areas, such as new processing plants, large equipment foundations, transport roads, or tailing dams, need flexible concrete production. A mobile plant is ideal for these.
- Rental Companies: Mobile batching plants are very popular in the equipment rental market. They have high rental demand. They offer a good return on investment.
- Emergency Response and Disaster Relief: In urgent situations where infrastructure needs quick repair, a mobile plant can reach the site fast. It provides critical concrete support quickly.
FAQs
Q 1: What are the main mobile batching plant advantages over a stationary one?
A: The main mobile batching plant advantages are quick setup, easy relocation, and reduced concrete transport costs. It allows on-site concrete production for projects that move often or have temporary needs.
Q 2: What is the typical mobile batching plant capacity range?
A: Typical mobile batching plant capacity ranges from 25 cubic meters per hour to 120 cubic meters per hour. The ideal capacity depends on your project’s daily concrete demand and overall volume.
Q 3: How does a quick deployment batching plant save money?
A: A quick deployment batching plant saves money by reducing foundation costs and installation time. It also cuts concrete transport costs by producing on-site. This leads to faster project completion and lower overall expenses.
Q 4: What is the average mobile batching plant price compared to a stationary one?
A: The initial mobile batching plant price can vary. It might be higher per cubic meter of capacity than a small stationary plant. However, its lower setup, relocation, and transport costs often make it more economical for temporary or multi-site projects.
Q 5: What are the key points for mobile batching plant maintenance?
A: Key points for mobile batching plant maintenance include daily cleaning of the mixer and hoppers, regular lubrication of moving parts, and frequent inspection of wear parts. Also, check all electrical and hydraulic systems for optimal performance.