Bolted Silo
Silo Capacity:
50-2000 tons
A bolted silo is a type of storage equipment. Workers assemble it on site using bolts. It is made from pre-fabricated panels. These panels are curved plates and stiffeners. We make these parts in our factory. Then, we ship them to the site for assembly. This design is very good for transport, installation, removal, and maintenance.
As an expert in heavy equipment for many years, I know bulk material storage is very important. A bolted silo is a key part of our storage solutions. We provide these globally. They are popular in concrete batching plants. They are also used in mineral processing plants. They work well in all bulk powder and granule handling systems. They have unique advantages.
Table of Contents
- What Is the Main Difference Between Bolted and Traditional Welded Silos?
- Which Industrial Fields and Material Storage Types Are Suitable for Bolted Silos?
- What Main Modules Make Up a Bolted Silo?
- How Do You Choose a Bolted Silo That Fits Specific Materials and Capacities?
- What Common Industrial Bulk Materials Can a Bolted Silo Store?
- What Is the On-Site Installation and Deployment Process for a Bolted Silo?
- What Is the Price of a Bolted Silo?
- What Are the Daily Maintenance Points for a Bolted Silo?
- FAQs
What Is the Main Difference Between Bolted and Traditional Welded Silos?
A bolted silo is assembled with bolts on site. A traditional welded silo is built by welding large steel sections together. This is usually done on site. The main difference lies in how they are constructed. This affects their transport, installation, flexibility, and overall cost. Bolted silos offer a distinct set of advantages. These make them a preferred choice for many modern industrial needs.
Traditional welded silos are built as one large piece. This means they often need special transport. They also need extensive on-site welding. This can take a lot of time. It also needs highly skilled labor. Welded silos are very strong. They are good for permanent installations. But their lack of flexibility can be a problem. This is true for projects that move or need future changes.
Understanding the Structural Design and Benefits
A bolted silo divides the body into standard panels. These panels are curved steel plates. They also have reinforcing ribs. We make these parts at the factory. Then, we drill precise holes in them. Workers join the plates using high-strength bolts and special seals. This modular design means the silo ships in a “flat-pack” form. This saves a lot of space during transport. It lowers shipping costs, especially for large silos and international projects. This method also allows for much faster assembly on site. It does not need any on-site welding. This reduces reliance on specialized welders. It also shortens project timelines.
On the other hand, traditional welded silos arrive as large, pre-fabricated sections or are fully welded on site. Transporting these large sections can be complex. It may need oversized vehicle permits. On-site welding also creates smoke, noise, and fire risks. While a welded silo offers strong, seamless construction, its installation is less flexible. It is also harder to move or expand later. The bolted design also means the silo can be easily taken apart. Then, you can reassemble it at a new location. This makes it good for projects that end. It is also good for rental companies. This improves the use of your investment. Bolted silos usually have protective coatings applied in the factory. This ensures better, more uniform corrosion resistance. On-site welding can sometimes damage these coatings.
Feature | Bolted Silo | Traditional Welded Silo | Your Practical Meaning |
---|---|---|---|
Transport | Flat-pack, low volume, lower cost | Large sections, high volume, higher cost | Saves shipping money, especially for global projects |
Installation | No welding, fast assembly, less labor | On-site welding, slower, more specialized labor | Quicker project start, reduced labor costs |
Flexibility | Easy to move, reassemble, or expand | Fixed, hard to move or modify | Adapts to changing project needs, better ROI |
Surface Finish | Factory-applied, uniform coatings | On-site application, prone to damage | Better corrosion protection, longer lifespan |
Safety | Fewer on-site risks (no welding) | Welding risks (fire, fumes) | Safer construction environment |
Which Industrial Fields and Material Storage Types Are Suitable for Bolted Silos?
A bolted silo is very flexible and cost-effective. It is used widely across many B2B client groups and industries. It is especially good for storing bulk materials. These include powders and granules. Its design allows it to adapt to various project needs.
This silo is a top choice where fast setup, portability, and reliable storage are needed. It fits industries from construction to agriculture.
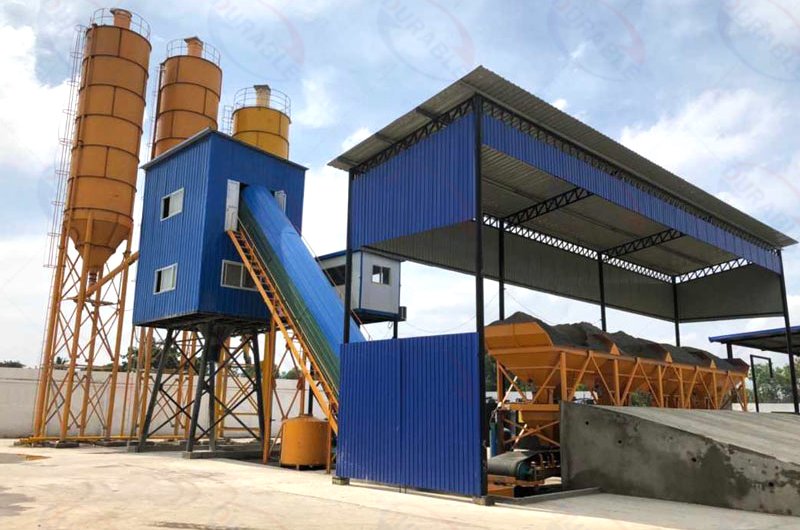
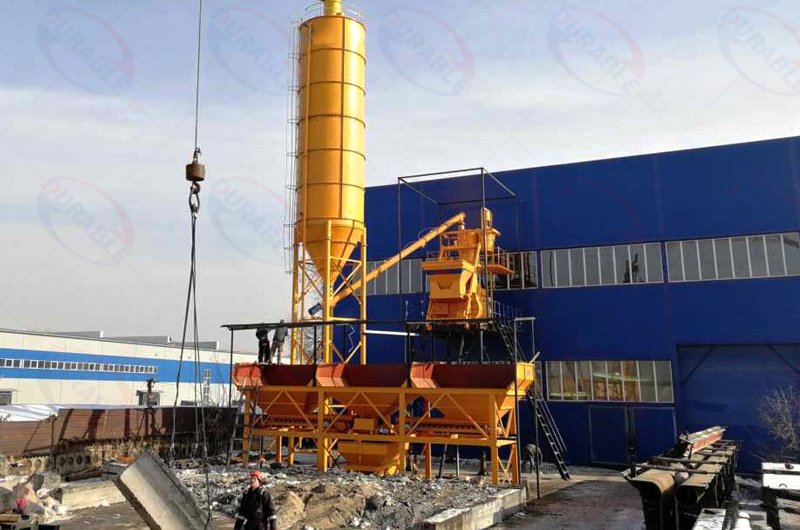
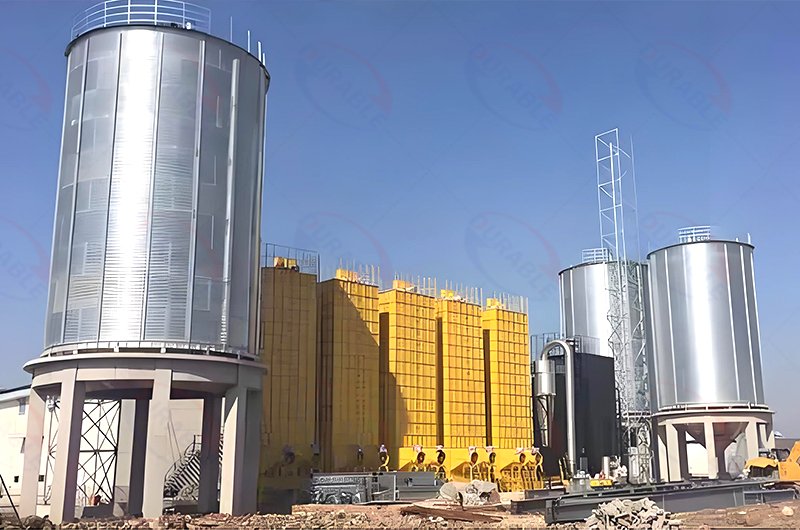
Versatile Storage Across Industries
Bolted silos are ideal for many applications. They are highly flexible and offer cost savings.
Concrete Batching Plants: They are mainly used to store bulk cement. They also store fly ash, slag powder, and other concrete binders. Their quick setup, take-down, and moving ability match the needs of mobile concrete batching plantsperfectly. They provide a reliable supply of key materials. This ensures continuous concrete production. This helps keep projects on schedule and within budget.
- Mineral Processing Plants: These silos store various metal or non-metal concentrates. These concentrates come from processes like flotation or magnetic separation. They also store auxiliary materials. These include lime powder for pH adjustment, bentonite, and barite powder. They can even store some processed dry tailings or industrial solid waste. The modular design means they can fit into existing plant layouts. They can also expand easily. This makes them a versatile storage solution for a range of raw materials and byproducts.
- Aggregate Producers: They store specific sizes of fine sand. They also store manufactured sand or stone powder. These materials are used in construction. Having on-site storage ensures a constant supply. This improves production efficiency.
- Cement Producers: They serve as intermediate storage. They also serve as finished cement silos. They ensure a steady flow of material in the production chain. They also hold the final product before shipment.
- Dry Mix Mortar Production Lines: They store cement, sand, and additives. These are raw materials for dry mix mortar. Precise storage helps maintain product quality.
- Building Material Industry: They store gypsum powder, lime powder, fly ash, glass powder, and clay. These materials are used to make various building products.
- Grain, Oil, Feed, and Fertilizer Industries: They store various bulk grains and powdered materials. This includes grains for food, animal feed, and chemical fertilizers. The sealed design protects the materials from moisture and pests.
- Environmental Industry: They store industrial waste. This includes fly ash and slag. This helps manage waste safely. It also helps meet environmental rules.
What Main Modules Make Up a Bolted Silo?
A typical bolted silo has several main parts. These parts are joined to form the complete storage unit. Understanding these modules helps you see how the silo works. It also shows why it is so adaptable. Its structure ensures safe and efficient bulk storage.
Each module is carefully designed. It works with others to create a strong and reliable storage solution. This modular approach is key to its flexibility and ease of assembly.
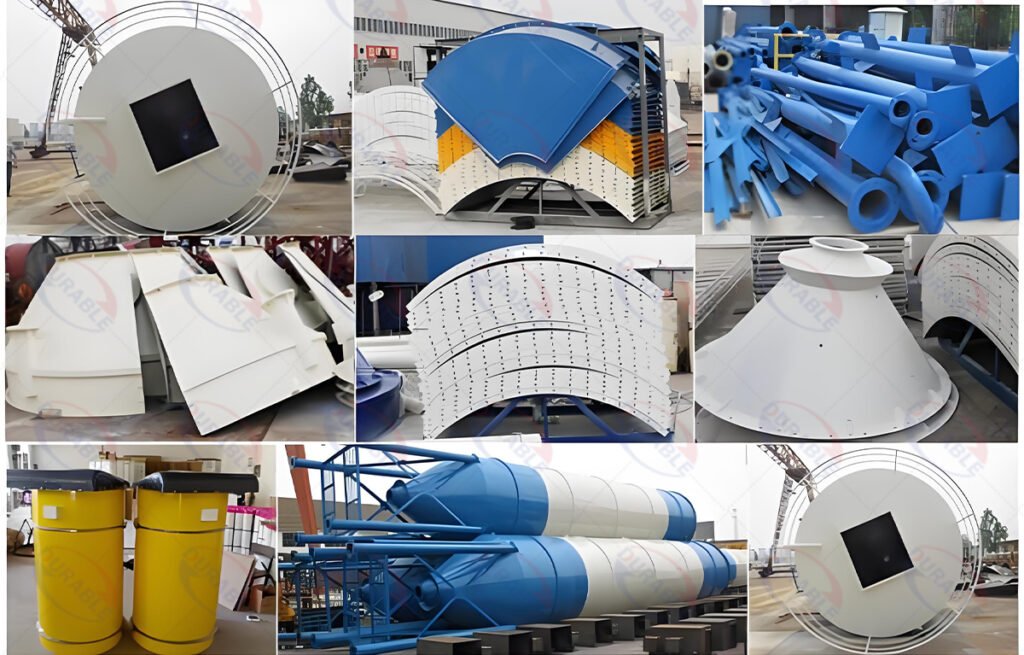
Core Structure and Components
A typical bolted silo mainly consists of these parts:
Cylinder Wall Panels: These are made from high-strength steel plates. We press and roll them into curved shapes. The surface gets anti-corrosion treatment. This includes sandblasting, priming, topcoats, or epoxy coating. The panels have precise holes. We connect them with high-strength bolts and special seals. This ensures a strong and sealed body.
- Stiffeners / Vertical Supports: These are placed along the silo body vertically. They make the silo more stable. They help it resist wind and earthquakes. They add crucial strength to the overall structure.
- Conical Bottom: This part helps materials flow out smoothly. It usually has a discharge opening. It may also have devices to help material flow. These devices include air hammers or fluidizing pads. They stop materials from clumping or arching. This ensures efficient unloading.
- Roof / Top Plate: This is often cone-shaped or domed. It has a manhole. It also has safety valves. It has a dust collector interface. It also has an inlet. This inlet usually connects to a screw conveyor.
- Support Legs / Frame: These hold the whole silo’s weight. They fix it to the foundation. They ensure the silo stands firm and upright.
- Accessory Systems: These are extra parts. They include level indicators to check material height. Arch breaking devices like air cannons or vibrators stop powder from blocking outlets. Safety valves balance pressure inside. This stops damage from too much or too little pressure. A dust collector on the roof gathers dust during feeding. This protects the environment. A ladder and handrails provide safe access for maintenance. A manhole allows for inside checks.
We design our bolted silos with our many years of experience. This experience comes from heavy equipment and material handling. Our silos have great transport ease. They are also cost-effective. Their modular design means “flat-pack shipment.” This reduces transport volume. It lowers international shipping costs a lot. This is especially true for big silos and global projects. They also allow for quick assembly. No site welding is needed. This shortens installation time. It reduces the need for expert welders. You can assemble them in days. This saves project time and labor costs. The bolt connections mean you can easily take the silo apart. You can reassemble it in a new place. This is good for projects that finish. It is also good for rental companies. This makes your equipment more useful.
How Do You Choose a Bolted Silo That Fits Specific Materials and Capacities?
Choosing the right bolted silo means matching its features to your exact needs. You must think about the material you will store. You also need to consider the required capacity. The right choice ensures efficient and safe bulk storage. It also helps to maximize your investment return.
Selecting the correct silo helps avoid common problems. These include material flow issues or capacity shortages. It ensures smooth operations for your industrial processes.
Technical Parameters
Capacity (t) | Diameter (mm) | Discharge Height (m) |
50 | 3260 | Customerized |
70 | 3260 | |
80 | 3260 | |
100 | 3260 | |
150 | 3600 | |
200 | 4500 | |
300 | 5050 | |
400 | 5500 | |
500 | 6600 | |
800 | 8000 | |
1000 | 8000 | |
1500 | 10000 | |
2000 | 12000 |
Factors for Proper Silo Selection
When choosing a bolted silo, several factors are critical:
Material Characteristics:
◦ Density: Heavy materials need stronger silo structures.
◦ Flowability: Some powders flow poorly. They might need a steeper cone bottom. They may also need arch breaking devices.
◦ Abrasiveness: Abrasive materials need wear-resistant liners.
◦ Moisture Sensitivity: Materials sensitive to moisture need a very tight seal. They also might need dehumidification.
◦ Corrosiveness: Corrosive materials need special coatings or stainless steel. This protects the silo.
- Required Capacity:
◦ Daily Consumption/Production: How much material do you use or produce daily?
◦ Buffer Stock: How many days of material do you need to store as a buffer? This depends on supply chain reliability.
◦ Delivery Frequency: How often do you receive new material shipments?
◦ Based on these, calculate the total volume needed. Then, choose a silo that meets this volume. Remember that bulk density varies. So, a silo rated for “X tons of cement” will hold a different volume of “Y tons of fly ash.” - Site Conditions:
◦ Space: Ensure there is enough space for the silo. Also, ensure space for its support structure.
◦ Ground Bearing Capacity: The ground must support the fully loaded silo’s weight.
◦ Wind/Seismic Zone: Silos in high wind or earthquake areas need stronger designs.
◦ Accessibility: Is the site accessible for transport and assembly equipment? - Discharge Method: How will the material be removed? This affects the cone design and accessory selection. For example, a screw conveyor or gravity discharge.
- Budget: Balance the silo’s cost with its features. Also consider the long-term benefits. These include reduced transport and installation costs.
Our engineering team works with you. We understand your material properties. We check your storage needs and site conditions. We offer a tailored solution. This includes the right silo capacity. It also includes the right structure and accessories.
What Common Industrial Bulk Materials Can a Bolted Silo Store?
Bolted silos are very versatile. They can store many common industrial bulk materials. These materials range from fine powders to granular substances. Their sealed design protects materials from moisture and contamination. This makes them suitable for a wide array of industries.
The ability to customize features like cone angle and internal linings makes them adaptable. They can store different materials. This versatility makes them a valuable asset. It is valuable for many manufacturing and processing operations.
Diverse Materials Stored in Bolted Silos
Bolted silos are widely used across industries to store many kinds of bulk materials.
Cement and Related Powders: This is one of the most common uses. Bolted silos frequently store:
◦ Cement: For concrete batching plants and construction.
◦ Fly Ash: A byproduct of coal combustion, used in concrete and other building materials.
◦ Slag Powder: Ground granulated blast-furnace slag, also used as a cement additive.
◦ Lime Powder (Calcium Oxide/Hydroxide): Used in mineral processing, water treatment, and construction.
- Aggregates and Sands:
◦ Fine Sand / Manufactured Sand: For concrete, mortar, and other building materials.
◦ Stone Powder / Crushed Fines: Byproducts of aggregate production, used as fillers or in concrete. - Mineral Powders:
◦ Various Mineral Concentrates: Such as iron ore concentrate, copper concentrate, lead/zinc concentrate from mineral processing plants.
◦ Bentonite: Used in drilling fluids, casting, and as a binder.
◦ Barite Powder: Used as a weighting agent in drilling muds.
◦ Gypsum Powder: Used in plaster, drywall, and cement production. - Chemicals and Fertilizers:
◦ Various powdered or granular chemical raw materials.
◦ Bulk fertilizers like urea, DAP, NPK. - Food and Feed Products:
◦ Grains (wheat, corn, rice).
◦ Flour and starch.
◦ Animal feed pellets.
◦ Sugar. - Industrial Byproducts/Waste:
◦ Fly ash (from power plants).
◦ Furnace slag.
◦ Wood pellets or sawdust.
The proper design ensures safe and efficient storage. It also allows for smooth discharge of each material. This requires careful consideration of the material’s flow properties. It also needs attention to its density and any corrosive nature.
What Is the On-Site Installation and Deployment Process for a Bolted Silo?
The on-site installation of a bolted silo is a key advantage. It is simpler and faster than welding a silo. The process is modular. This allows for efficient deployment. It quickly prepares the silo for bulk storage.
Understanding the steps helps you plan your project better. It ensures a smooth and safe setup. This maximizes the benefits of its modular design.
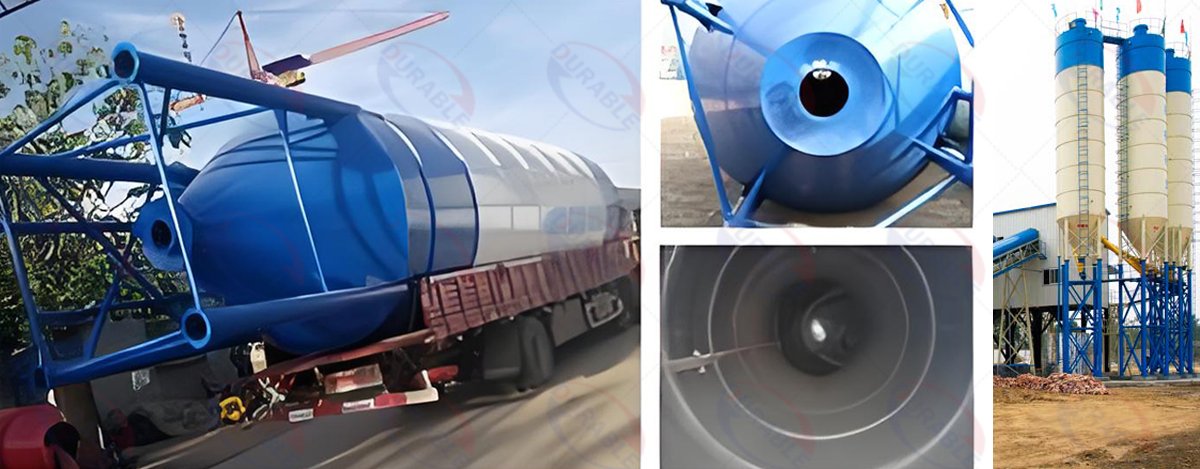
Steps for Fast Silo Assembly and Deployment
The deployment process for a bolted silo is designed for speed and ease.
Site Preparation: 1.First, you must prepare the site. This involves leveling the ground. You must also build a concrete foundation. This foundation has anchor bolts. The bolts match the silo’s support structure. The ground must be firm. It must support the fully loaded silo’s weight.
- Component Arrival and Unloading: The silo components arrive on site. They come in flat-pack containers. This includes the curved panels, stiffeners, cone sections, roof parts, and accessories. These parts are then carefully unloaded. They are laid out for easy access.
- Base Ring Assembly: Workers start by assembling the bottom ring of the silo. They use the numbered panels. They bolt them together on the foundation. High-strength bolts and special sealant strips are used. This ensures a tight seal.
- Sequential Ring Assembly: They then build subsequent rings. They lift each new ring. They place it on top of the one below. They secure it with bolts. This process continues upwards. It uses small cranes or lifting equipment.
- Cone and Roof Installation: After the main cylinder body is done, the conical bottom is attached (if it is a separate module). Then, the roof section is lifted into place. It is bolted to the top ring. This step also includes installing the manhole, safety valves, and inlet connections.
- Accessory and Support Installation: Next, workers install the support legs or frame. They also put in the ladder, handrails, level indicators, and dust collector. They connect any necessary piping and electrical wiring.
- Final Checks and Commissioning: Once assembled, a thorough check is done. This ensures all bolts are tight. All seals are secure. All accessories work correctly. Then, the silo is ready for commissioning. This includes testing its functionality before first use.
This step-by-step assembly process minimizes the need for heavy machinery. It also reduces complex on-site fabrication. This makes deployment much faster. It also lowers labor costs.
What Is the Price of a Bolted Silo?
The price of a bolted silo varies a lot. It depends on several key factors. These include its capacity, the materials it’s made from, and any special features. Understanding these factors helps you get an accurate quote. It also helps you assess the overall value.
While direct pricing is complex without specific needs, we can discuss the elements that influence the cost. This helps you plan your budget. It also helps you understand the return on investment.
Factors Influencing Bolted Silo Cost
The silo price is not a single number. It is influenced by these points:
- Capacity: This is the biggest factor. Larger silos need more steel panels and components. So, they cost more. A 50-ton cement silo will be much cheaper than a 500-ton one.
- Material and Coating:
◦ Steel Type: Standard carbon steel is common. Stainless steel costs more. It is used for corrosive materials or food-grade storage.
◦ Anti-Corrosion Treatment: The type of surface treatment greatly impacts price. Options include standard painting, multi-layer epoxy coatings, or hot-dip galvanizing. Higher quality coatings cost more. But they offer better protection and longer life. - Cone Bottom Type: The discharge cone design affects cost. A standard 45-degree cone is typical. A steeper 60-degree cone for poorly flowing materials costs more. Special designs with fluidizing systems also add to the price.
- Accessories and Automation: Adding features increases the cost. These features include:
◦ Dust collectors: Essential for environmental compliance.
◦ Level indicators: For precise material monitoring.
◦ Arch breaking devices (e.g., air cannons, vibrators): For sticky materials.
◦ Safety valves: For pressure control.
◦ Weighing systems: To turn the silo into a batching scale.
◦ Ladders, platforms, and manholes are standard. But complex access systems can add cost. - Design and Customization: Standard models are more cost-effective. Custom designs for unique materials or site constraints cost more. This includes special dimensions or unusual material inlets/outlets.
- Transportation Costs: While bolted silos are efficient to ship, the distance from our factory to your site still adds to the total cost. Longer distances mean higher freight charges.
- Installation Services: We offer installation guidance. If you need our team for full on-site assembly, this will be an added service cost. Many clients use local labor with our guidance to save money.
A bolted silo generally offers excellent value. This is due to its low transport costs and quick installation. While the initial purchase varies, its overall long-term cost of ownership is often lower. This is compared to a traditional welded silo.
What Are the Daily Maintenance Points for a Bolted Silo?
Daily maintenance is vital for your bolted silo. It ensures the silo operates safely. It also extends its lifespan. Regular care prevents costly breakdowns. It also helps maintain material quality inside.
Proper maintenance is simple. It involves routine checks and specific actions. These steps keep your silo in top working order. They also help secure your investment in bulk storage.
Essential Care for Your Silo
To keep your bolted silo running well, follow these key maintenance points:
Daily Visual Inspection:
◦ Check for any visible damage to the silo body. Look for dents, cracks, or signs of wear.
◦ Inspect all bolted connections. Look for any loose bolts or signs of material leakage around the seams. This is very important for a bolted silo.
◦ Check the condition of the exterior coating. Look for peeling paint or rust.
◦ Examine the support structure and foundation for any shifts or cracks.
◦ Ensure all safety features are in place and undamaged. This includes ladders, handrails, and guards.
- Check Accessory Systems:
◦ Dust Collector: Check the dust collector. Ensure it is working correctly. Empty the dust bin if it is full. Clean filters regularly to maintain efficiency.
◦ Level Indicators: Verify that the level indicators are giving accurate readings.
◦ Arch Breaking Devices: For silos storing sticky materials, test arch breaking devices (like air hammers or vibrators) regularly. Ensure they prevent material blockages.
◦ Safety Valves: Ensure safety valves are clear and able to open and close freely. This is crucial for pressure balance. - Material Flow Monitoring:
◦ Observe the material discharge. Ensure it is smooth and consistent.
◦ Listen for any unusual noises during material flow or discharge. - Cleaning:
◦ Keep the area around the silo base clean. Remove any spilled material. This prevents buildup and pest issues.
◦ Clean dust from the silo top and ladder access points. - Lubrication (if applicable): If any accessories have moving parts that need lubrication (e.g., some types of level indicators or rotary valves), follow the manufacturer’s lubrication schedule.
- Documentation: Keep a maintenance log. Record all checks, issues found, and actions taken. This helps track the silo’s history. It also helps plan future maintenance.
FAQs
Q 1: What is the average silo price for a standard 100-ton cement silo?
A: The average silo price for a standard 100-ton cement silo varies. It depends on factors like material quality, coating type, and accessories. A typical range might be from Y, but a detailed quote is needed for specifics.
Q 2: How long does bolted silo installation typically take?
A: Bolted silo installation can take anywhere from 3 to 7 days for a standard model. This depends on the silo size, the site conditions, and the experience of the assembly team. Larger silos may take slightly longer.
Q 3: Can a bolted silo be moved after it’s been installed?
A: Yes, a bolted silo can be easily disassembled. You can then move it to a new location. Then, you can reassemble it. This flexibility is a major advantage over traditional welded silos.
Q 4: What kind of bulk materials silo is most cost-effective for long-term storage?
A: A bolted silo is often the most cost-effective bulk materials silo for long-term storage. This is due to its low transport costs, quick installation, and excellent durability. It also has easy maintenance.
Q 5: What should I consider for silo maintenance in harsh climates?
A: For silo maintenance in harsh climates, focus on coating integrity and seal condition. Regular checks for wear and corrosion are vital. Use specialized coatings if needed. Ensure the silo can withstand extreme temperatures and winds.