Diesel Drum Mixer
Charging Volume(L):
560 and 750
Discharging Volume(L):
350 and 500
As an expert in heavy equipment and building materials for many years, I understand concrete mixer functions. I also know their uses very well. The diesel drum mixer is a classic and vital machine in our concrete mixer range. It has unique strengths. It holds an important place for specific jobs and customers.
A diesel drum mixer is a small, easy-to-move gravity-type concrete mixer. It uses the rotation of its drum. It also uses internal mixing blades. These blades tumble the materials. This makes concrete mix under gravity. Its main feature is using a diesel engine. This makes it work on its own. This is true even in remote areas without stable power.
Table of Contents
- How Do Diesel Drum Mixers Work Differently from Electric Mixers?
- Which Construction Scenarios and Projects Are Best for Diesel Drum Mixers?
- How Do You Choose the Right Diesel Drum Mixer Model for Your Project Needs?
- How Do You Evaluate Diesel Drum Mixer Fuel Efficiency and Daily Maintenance Costs?
- What Performance Indicators and Features Are Most Important When Choosing a Diesel Drum Mixer?
- Investing in a Diesel Drum Mixer: How to Measure Its Portability and Long-Term Value?
- FAQs
How Do Diesel Drum Mixers Work Differently from Electric Mixers?
A diesel drum mixer operates differently from an electric mixer. Its core working principle is gravity. It also uses diesel power. This makes it a self-contained mixer. It works without external power. This is a key difference.
This difference makes it perfect for places where electricity is scarce. It gives you the power you need, anywhere you need it.
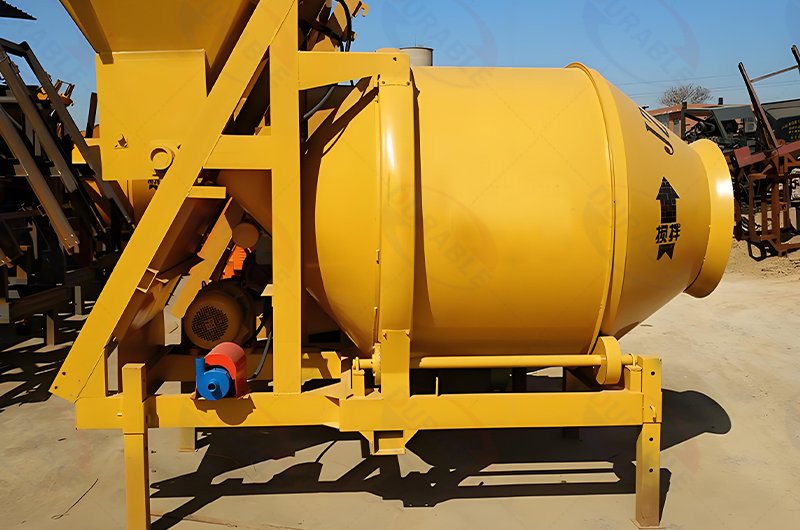
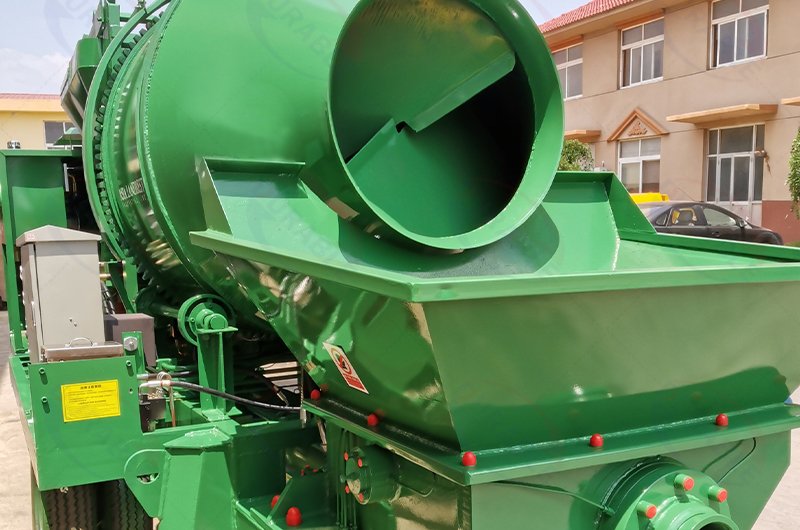
Understanding Mixing Principles and Power Sources
The diesel drum mixer uses a gravity-fed mixing method. Inside the drum, there are mixing blades or spiral vanes. As the drum rotates at a tilt, the materials like cement, sand, gravel, and water are lifted. Gravity then pulls them down. At the same time, the materials tumble, collide, and spread inside the drum. This action mixes them evenly. This mixing is gentle. It does not easily damage aggregates. It mainly mixes plastic and semi-plastic concrete. It also mixes mortar well.
The power source is a diesel engine. This engine drives the mixing drum’s rotation through a gearbox. It also controls the drum’s tilt angle. This independent power supply frees the mixer from relying on the electric grid. This greatly extends where you can use it. This makes it ideal for off-grid concrete projects.
In contrast, electric mixers use an electric motor. This motor needs a stable power supply. This usually comes from a mains connection or a generator. Electric mixers can be drum mixers or forced mixers. Forced mixers use paddles to churn the material. Electric mixers are common on sites with reliable power. They often have lower running noise. They also have zero emissions at the point of use.
The main difference is the power source. Diesel mixers offer total independence. Electric mixers offer steady power with less noise. For remote site concrete mixing, the diesel option is often the only choice. It provides the necessary power without needing external infrastructure.
Feature | Diesel Drum Mixer | Electric Mixer | Your Direct Benefit |
---|---|---|---|
Power Source | Diesel engine, fully independent | Electric motor, needs power grid/gen | Freedom to work anywhere vs. quieter operation |
Mobility | Highly portable, no power cable | Portable but needs power access | Work in remote areas vs. clean power source |
Best Use | Off-grid, remote, rural sites | Sites with stable power access | Versatility in location vs. consistent power |
Emissions | Exhaust emissions | Zero emissions at point of use | Works anywhere vs. cleaner local air |
Which Construction Scenarios and Projects Are Best for Diesel Drum Mixers?
A diesel drum mixer is best for specific construction scenarios. These are usually places where power is not readily available. Its independent power source makes it ideal for remote site concrete mixing. It shines in jobs far from urban centers.
This mixer is a versatile tool. It brings concrete production directly to the most challenging locations. It is perfect for smaller jobs and repair work.
Ideal Locations for Independent Operation
The diesel drum mixer is excellent for these B2B customer groups:
- Small to Medium Construction Contractors: They take on projects like building houses, expanding workshops, or making small roads. They also work on bridges, walls, and foundations. These jobs often happen in new development areas. These areas might lack a steady power supply.
- Rural Construction and Village Renovation Projects: These areas often have unstable electricity. They need concrete mixers that can work independently. This mixer provides the necessary flexibility for rural construction concrete.
- Remote Area Engineering Projects: This includes water conservation projects. It also includes auxiliary work in mining areas. It is used for building power transmission line towers. These sites are typically far from urban infrastructure. They need off-grid concrete solutions.
- Road Maintenance and Repair Teams: These teams need to produce small batches of concrete quickly. This is for road repairs or slope protection. The mixer’s portability allows them to move fast. They can set up right where the work is needed.
- Equipment Rental Companies: This mixer is a vital part of their rental fleet. It meets the temporary or small-scale needs of various clients. Many small contractors rent them for short projects.
- Small Precast Component Workshops: These workshops produce small amounts of precast items. This includes concrete blocks or paving bricks. They might not need a large, permanent batching plant.
In these situations, the diesel drum mixer’s ability to operate independently is a huge advantage. It saves time and money. It avoids the need for costly power connections or large generators. It is a reliable choice for any project needing flexible, on-site concrete production. It makes concrete possible even in the toughest spots.
How Do You Choose the Right Diesel Drum Mixer Model for Your Project Needs?
Choosing the right diesel drum mixer model is important. It means matching the mixer’s features to your project’s demands. This ensures efficient concrete mixer operation. It helps you produce the exact amount of concrete you need.
The correct choice optimizes your work. It helps you manage costs. It also ensures the mixer lasts a long time.
Concrete Mixer-JZC/JZM Series
Item | Charging Capacity | Discharging Capacity | Productivity | Aggregate Size | Overall Dimension |
JZC250 | 350L | 250L | 7- 10m3/h | 60mm | 3930x2040x3140mm |
JZC350A | 560L | 350L | 10-14m3/h | 60mm | 4010x2140x3340mm |
JZC350B | 560L | 350L | 10- 14m3/h | 60mm | 4010x2140x3340mm |
JZC500 | 800L | 500L | 18-20m3/h | 60mm | 5230x2300x5450mm |
JZM500 | 800L | 500L | 18-20m3/h | 60mm | 5130x2400x5550mm |
JZM750 | 1200L | 750L | 20-22.5m3/h | 60mm | 6107x2050x6070mm |
Factors for Mixer Model Selection
When selecting a diesel drum mixer model, consider these key factors:
- Required Concrete Output (Capacity):
◦ Batch Size: What is the volume of concrete you need per batch? Our mixers come in sizes like 100L, 200L, 350L, and 500L. Choose a size slightly larger than your usual batch. This gives flexibility.
◦ Hourly Output: How many cubic meters of concrete do you need per hour? This depends on batch size and mixing cycle time. Match this to your project’s peak demand. Avoid choosing a mixer that is too small. That can slow down your project. An undersized mixer can cause delays. - Mobility Needs:
◦ Portability: Do you need a portable concrete mixer that can be easily moved by hand? Or do you need a mobile concrete mixer that can be towed by a vehicle for longer distances? Consider the type of wheels and chassis. Some models are lighter. Some have stronger towing bars.
◦ Site Terrain: If your site has rough terrain, choose a model with robust tires and a durable frame. - Diesel Engine Power:
◦ Engine Horsepower: Ensure the diesel engine has enough power for your largest batch. A more powerful engine handles tougher mixes better. It also ensures reliable starting in varying conditions.
◦ Fuel Consumption: While all diesel engines consume fuel, some are more efficient. Consider the engine brand and its reputation for fuel economy. We will discuss this more later. - Type of Concrete to Mix:
◦ Plastic/Semi-Plastic Concrete: Diesel drum mixers are best for these types. If you need very dry or stiff concrete, a forced mixer might be better.
◦ Aggregate Size: Most drum mixers handle common aggregate sizes. If you have very large aggregates, check the drum and paddle design. - Budget: Consider the initial purchase price. Also, think about long-term operating costs. These include diesel mixer fuel consumption and mixer maintenance.
- Ease of Operation and Maintenance: Look for simple controls. Also, look for easy access for cleaning and servicing. This saves labor time.
- Build Quality: Check the quality of the steel used for the drum and frame. Also, check the durability of the transmission system. This ensures the mixer lasts through tough job conditions.
By carefully evaluating these points, you can select the most suitable diesel drum mixer. It will efficiently meet your specific project requirements.
How Do You Evaluate Diesel Drum Mixer Fuel Efficiency and Daily Maintenance Costs?
Evaluating diesel drum mixer fuel efficiency and daily maintenance costs is crucial. It helps you understand the true cost of owning and operating the machine. This is important for construction equipment rental companies or long-term projects. Understanding these costs helps you manage your budget.
These factors directly impact your project’s profitability. Smart choices here lead to significant savings.
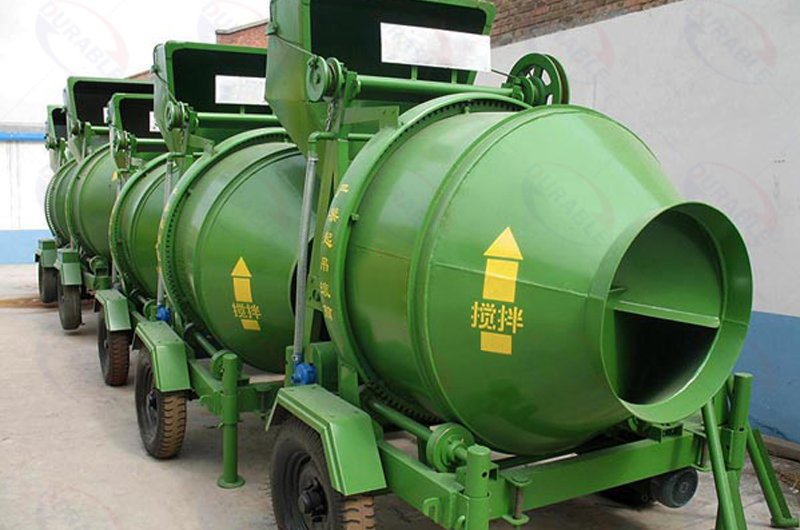
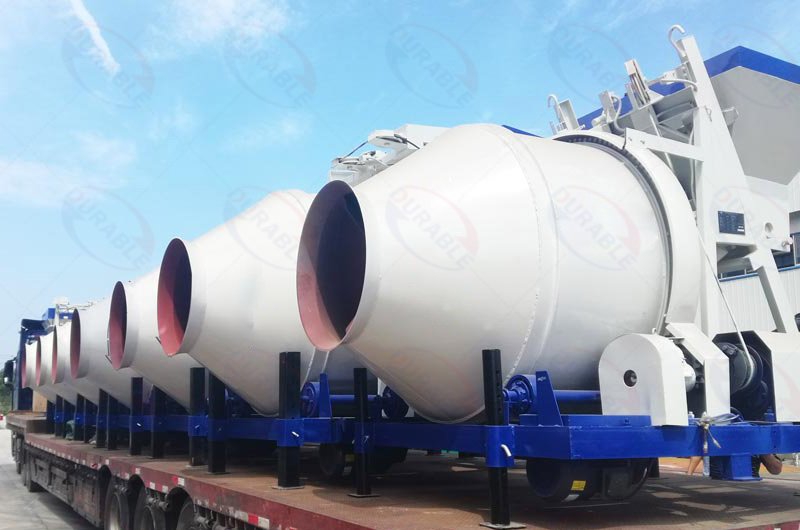

Managing Operational Costs Effectively
Evaluating the fuel efficiency and maintenance costs of a diesel drum mixer involves looking at several factors:
- Diesel Mixer Fuel Consumption:
◦ Engine Efficiency: Modern diesel engines are more fuel-efficient. Look for mixers with reputable engine brands known for lower fuel use. Engine size also plays a role. A smaller engine might save fuel if it matches the load.
◦ Load and Operating Time: Fuel consumption increases with heavier loads and longer operating hours. Estimate your typical daily operating time.
◦ Mixer Capacity: Larger mixers generally use more fuel per hour. But they might use less fuel per cubic meter of concrete if they finish batches faster. Calculate fuel cost per cubic meter. This gives a clearer picture.
◦ Maintenance Impact: A well-maintained engine runs more efficiently. Regular filter changes and tuning reduce fuel waste. - Daily Maintenance Costs:
◦ Simplicity of Design: Diesel drum mixers are usually simple. They have fewer complex parts than forced mixers. This means less can go wrong. Maintenance is generally straightforward.
◦ Wear Parts: The main wear parts are the mixing drum’s internal blades and the drum itself. These are typically durable steel. Replacement is usually needed less often than for forced mixer paddles. Check the quality of these parts. High-quality steel means longer life.
◦ Engine Maintenance: Diesel engines need regular oil changes, filter replacements (fuel, oil, air), and occasional tune-ups. These are standard costs for any diesel engine.
◦ Cleaning: Daily cleaning is essential. It prevents concrete buildup. This reduces wear on the drum and blades. It also makes the mixer last longer.
◦ Lubrication: Regular greasing of bearings and moving parts is cheap. It prevents costly repairs.
◦ Accessibility: Check how easy it is to access parts for maintenance. Easier access means less labor time.
We provide clear guidance on expected fuel consumption for our models. We also offer detailed mixer maintenance schedules. This helps you plan and manage your operational budget effectively.
What Performance Indicators and Features Are Most Important When Choosing a Diesel Drum Mixer?
When choosing a diesel drum mixer, certain performance indicators and features are very important. They tell you how well the mixer will work for your needs. Paying attention to these details helps ensure efficient concrete mixer operation. It also guarantees the quality of your concrete.
Focusing on these key aspects helps you make a smart investment. It ensures the mixer will perform reliably on your job site.
Key Aspects for Optimal Mixer Selection
When choosing a diesel drum mixer, focus on these performance indicators and features:
- Mixing Quality for Gravity Mixers:
◦ Drum Design: A well-designed drum ensures efficient material tumbling. The shape and internal blades affect mixing uniformity. Look for smooth interiors that prevent material sticking.
◦ Mixing Speed (RPM): The rotational speed of the drum impacts mixing. Too fast can cause segregation. Too slow can increase mixing time. The optimal RPM ensures proper lifting and falling of materials.
◦ Mixing Cycle Time: While gravity mixers are slower than forced mixers, a good drum mixer should still achieve a plastic concrete mix within a reasonable time (e.g., 3-5 minutes per batch). This affects overall throughput. - Engine Reliability and Power:
◦ Reputable Engine Brand: Choose a mixer with a well-known diesel engine brand. These engines are usually more reliable and have better parts availability.
◦ Starting Capability: The engine should start easily in various temperatures.
◦ Sufficient Horsepower: Ensure the engine has enough power to handle the maximum drum load without strain. This prevents breakdowns and ensures consistent mixing speed. - Durability and Build Quality:
◦ Steel Thickness: The thickness of the steel used for the drum, frame, and chassis indicates durability. Thicker steel means it can withstand more abuse.
◦ Welding Quality: High-quality welding ensures structural integrity. Poor welds can lead to cracks.
◦ Bearing and Gearbox Quality: These are critical for long-term operation. High-grade bearings and a robust gearbox reduce maintenance and extend life.
◦ Wear-Resistant Blades: While drum mixers have fewer wear parts than forced mixers, the internal mixing blades still need to be durable. They should be made from wear-resistant materials. - Portability and Mobility Features:
◦ Wheel Type and Size: Large, pneumatic tires are better for rough terrain. Solid tires are good for stable, flat surfaces.
◦ Tow Bar/Handle Design: A strong, ergonomic tow bar or handle makes moving the portable concrete mixer easier.
◦ Compactness: A smaller footprint is always better for transport and tight job sites. This is a key benefit of a small concrete mixer. - Ease of Operation and Maintenance:
◦ Simple Controls: Controls should be straightforward, making concrete mixer operation easy for various skill levels.
◦ Accessible Components: Parts needing regular maintenance, like engine filters or grease points, should be easy to reach.
◦ Discharge Mechanism: Check if the drum tilting mechanism (handwheel, hydraulic) is smooth and reliable.
By prioritizing these performance indicators and features, you can ensure your diesel drum mixer is a productive and reliable asset for your construction projects.
Investing in a Diesel Drum Mixer: How to Measure Its Portability and Long-Term Value?
Investing in a diesel drum mixer involves more than just the purchase price. You must measure its portability. You also need to look at its long-term value. These factors are crucial. They impact your project efficiency. They also affect your return on investment.
A portable concrete mixer offers unique benefits. These benefits lead to significant long-term gains. They are especially true for certain types of projects.
Assessing Mobility and Sustained Benefits
Measuring the portability and long-term value of a diesel drum mixer involves these considerations:
- Portability Measurement:
- Weight and Dimensions: A lighter, more compact mixer is easier to load, transport, and maneuver on site. Check its total weight. Look at its overall footprint.
- Wheel Design: Large, durable wheels are essential for easy movement. Pneumatic tires are good for rough ground. Solid tires are good for harder surfaces.
- Tow Bar/Handles: A strong, well-designed tow bar or handles makes pulling or pushing easier.
- Balance: A well-balanced mixer is easier to tilt and move.
- Ease of Loading: Can it be easily loaded onto a truck or trailer? Some models have lifting points. This makes them easier to handle with cranes.
- Long-Term Value Assessment:
- Versatility in Application: The mixer’s ability to operate in any location (due to diesel power) provides immense value. This opens up opportunities for off-grid concrete projects or remote jobs. It means you are not limited by power access.
- Durability and Lifespan: A robustly built diesel drum mixer will last for many years. This is true even with regular use in tough conditions. High-quality steel, reliable engines, and durable components contribute to a longer service life. This reduces the need for frequent replacements.
- Low Operating Costs: As discussed, its simple design and efficient diesel engine can result in lower daily operating costs. This is true compared to larger, more complex mixers. The lower diesel mixer fuel consumption and easy mixer maintenance contribute to this.
- Rental Market Value: If you are in the construction equipment rental business, a reliable portable concrete mixer with a diesel engine is highly desirable. It has good rental demand. Its low maintenance makes it a profitable asset.
- Resale Value: Well-maintained, quality diesel drum mixers hold their value well in the used equipment market.
- Reduced Logistics Costs: Being able to mix concrete on site, especially in remote areas, saves on transport costs for ready-mix concrete. This is a significant long-term saving.
- Project Flexibility: Owning a mobile concrete mixer gives you the flexibility to take on diverse projects. It ensures you can meet concrete needs anywhere. This is especially true for rural construction concrete where power is scarce.
By considering both the immediate portability and the enduring value of a diesel drum mixer, you can make a strategic investment. It will support your operations for years to come.
FAQs
Q 1: What makes a diesel drum mixer ideal for off-grid concrete projects?
A: A diesel drum mixer is ideal for off-grid concrete projects because its built-in diesel engine provides independent power. It does not need external electricity. This allows concrete mixing anywhere, even in remote areas.
Q 2: How does diesel mixer fuel consumption compare to electric mixers?
A: Diesel mixer fuel consumption incurs direct fuel costs. Electric mixers have electricity costs. Diesel mixers offer complete site independence. Electric mixers need a power source, like a generator, which also consumes fuel.
Q 3: Is a portable concrete mixer easy to move by one person?
A: A portable concrete mixer varies in ease of movement. Smaller models (100-200L) can often be moved by one person. Larger ones (350L+) might need two people or a vehicle for towing. Always check the weight and features.
Q 4: What kind of mixer maintenance is typical for a diesel drum mixer?
A: Typical mixer maintenance for a diesel drum mixer includes daily cleaning of the drum, regular lubrication of moving parts, and routine engine checks (oil, fuel, air filters). Also, inspect the drum’s internal blades for wear.
Q 5: Can a small concrete mixer be used for continuous operation on a small project?
Yes, a small concrete mixer can be used for continuous operation on a small project. While its capacity is limited, its reliability and independent power make it suitable for consistent, small-batch production throughout the workday.